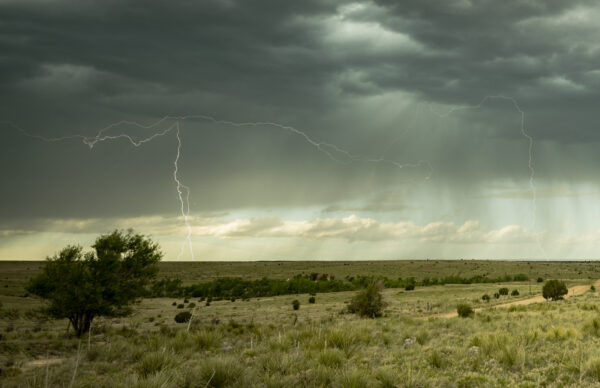
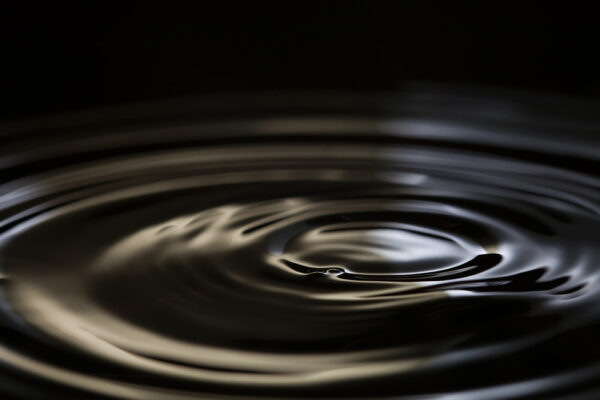
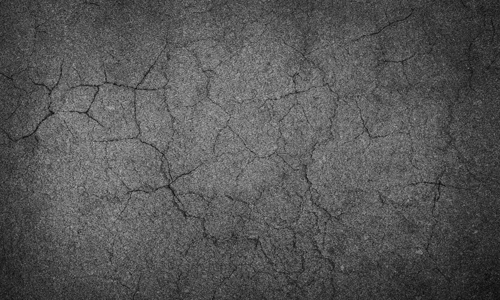
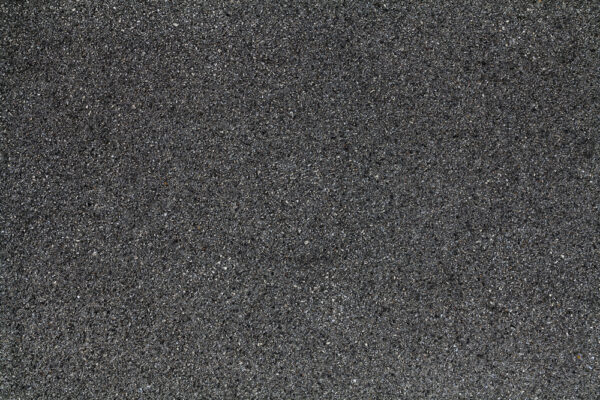
Our Asphalt Shingles vs. Standard Asphalt Shingles
NEX® Polymer Modified Asphalt outperforms traditional oxidized asphalt.
Standard shingles are made of an old technology called Oxidized Asphalt which uses oxygen and extreme heat to harden asphalt so that it can be used in a shingle. Like over-baking a cookie, the extreme heat of the oxidation process dries-out the asphalt core of the shingle, robbing it of its natural suppleness and stickiness which is why standard shingles prematurely become brittle, crack, and lose granules.
Malarkey pioneered Polymer Modified Asphalt. Our NEX® formula uses rubber polymers, also known as SBS (Styrene-Butadiene-Styrene), and plastic polymers, to chemically harden and rubberize the asphalt core of the shingle.
NEX® preserves asphalt’s natural suppleness and stickiness to resist thermal dry-out and improve granule embedment, and adds rubberlike strength and flexibility to resist tears, withstand wind, and absorb and deflect force impact to help prevent hail damage.